Full Paper View Go Back
Development of Process Technology for Making Electrode Quality Steel through Continuous Casting
Kumar Abhishek1 , Rajib Khanda2 , Somnath Kumar3 , Avinash Mishra4 , Sanjay Kumar Dhua5
Section:Research Paper, Product Type: Journal-Paper
Vol.6 ,
Issue.10 , pp.24-31, Oct-2020
Online published on Oct 31, 2020
Copyright © Kumar Abhishek, Rajib Khanda, Somnath Kumar, Avinash Mishra, Sanjay Kumar Dhua . This is an open access article distributed under the Creative Commons Attribution License, which permits unrestricted use, distribution, and reproduction in any medium, provided the original work is properly cited.
View this paper at Google Scholar | DPI Digital Library
How to Cite this Paper
- IEEE Citation
- MLA Citation
- APA Citation
- BibTex Citation
- RIS Citation
IEEE Style Citation: Kumar Abhishek, Rajib Khanda, Somnath Kumar, Avinash Mishra, Sanjay Kumar Dhua, “Development of Process Technology for Making Electrode Quality Steel through Continuous Casting,” International Journal of Scientific Research in Multidisciplinary Studies , Vol.6, Issue.10, pp.24-31, 2020.
MLA Style Citation: Kumar Abhishek, Rajib Khanda, Somnath Kumar, Avinash Mishra, Sanjay Kumar Dhua "Development of Process Technology for Making Electrode Quality Steel through Continuous Casting." International Journal of Scientific Research in Multidisciplinary Studies 6.10 (2020): 24-31.
APA Style Citation: Kumar Abhishek, Rajib Khanda, Somnath Kumar, Avinash Mishra, Sanjay Kumar Dhua, (2020). Development of Process Technology for Making Electrode Quality Steel through Continuous Casting. International Journal of Scientific Research in Multidisciplinary Studies , 6(10), 24-31.
BibTex Style Citation:
@article{Abhishek_2020,
author = {Kumar Abhishek, Rajib Khanda, Somnath Kumar, Avinash Mishra, Sanjay Kumar Dhua},
title = {Development of Process Technology for Making Electrode Quality Steel through Continuous Casting},
journal = {International Journal of Scientific Research in Multidisciplinary Studies },
issue_date = {10 2020},
volume = {6},
Issue = {10},
month = {10},
year = {2020},
issn = {2347-2693},
pages = {24-31},
url = {https://www.isroset.org/journal/IJSRMS/full_paper_view.php?paper_id=2128},
publisher = {IJCSE, Indore, INDIA},
}
RIS Style Citation:
TY - JOUR
UR - https://www.isroset.org/journal/IJSRMS/full_paper_view.php?paper_id=2128
TI - Development of Process Technology for Making Electrode Quality Steel through Continuous Casting
T2 - International Journal of Scientific Research in Multidisciplinary Studies
AU - Kumar Abhishek, Rajib Khanda, Somnath Kumar, Avinash Mishra, Sanjay Kumar Dhua
PY - 2020
DA - 2020/10/31
PB - IJCSE, Indore, INDIA
SP - 24-31
IS - 10
VL - 6
SN - 2347-2693
ER -
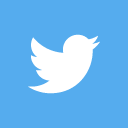
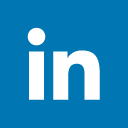
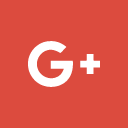
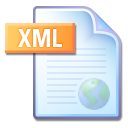
Abstract :
The electrode welding non rimming grade (EWNR) is one such grade in which carbon (C), silicon (Si) and aluminium (Al) contents are very low. Electrode quality steel wire rods are used for making core wire for covered electrodes. Covered electrodes are used in manual metal arc welding (MMAW) of mild steel. There are two variants of electrode quality steel: electrode welding rimming (EWR), which are rimming steel and made through the twin hearth furnace (THF)-ingot casting route; and EWNR, which are de-oxidized steel and made through the basic oxygen furnace (BOF) - continuous casting route. Before the advent of continuous casting, the electrode quality steel was made through ingot casting throughout the world. Because of the obvious advantages offered by the BOF-continuous casting route over the THF-ingot casting route, steel plants across the world have shifted to the continuous casting process. Therefore, to fulfill the demand of electrode quality steel, steelmakers were left with no choice but to make this grade through continuous casting. However, unlike its predecessor, the continuous casting process suffers with the lacuna of inability to make rimming steel grades. The present paper lays down the challenges encountered in making the non-rimming variant of electrode quality steel through continuous casting, along with the methods devised to mitigate those challenges.
Key-Words / Index Term :
electrode quality, covered electrode, core wire, EWNR, de-oxidation, silicon reversal
References :
[1] Mild Steel for Metal Arc Welding Electrodes, IS 2879:1998, Bureau of Indian Standards (BIS), New Delhi, 1998.
[2] R.E. Lino, A.M.F. Marins, L.A. Marchi, J.A. Mendes, L.A. Penna, J.G. Costa Neto, J.H.A. Caldeira and A.V. Costa e Silva, “Influence of the chemical composition on steel casting performance,” Journal of Materials Research and Technology (JMR&T), Vol. 6, Issue 1, pp. 50-56, 2017.
[3] S. Abdelaziz, G. Megahed, I. El-Mahallawi and H. Ahmed, “Control Ca addition for improved cleanness of LCAK steel,” Ironmaking and Steelmaking, Vol. 36, Issue 6, pp. 432-441, 2009.
[4] Hot Rolled Medium and High Tensile Structural Steel, IS 2062:2011, Bureau of Indian Standards (BIS), New Delhi, 2011.
[5] W. Yang, L. Zhang, X. Wang, Y. Ren, X. Liu and Q. Shan, “Characteristics of Inclusion in Low Carbon Al-killed Steel during Ladle Furnace Refining and Calcium Treatment,” ISIJ International, Vol. 53, Issue 8, pp. 1401-1410, 2013.
[6] The Welding Institute (TWI) (n.d.) Characteristics of steels from different deoxidation methods. Available at: https://www.twi-global.com/technical-knowledge/faqs/faq-what-are-the-distinguishing-characteristics-of-steels-made-using-different-deoxidation-practices.
[7] J. Ikäheimonen, K. Leiviskä, J. Ruuska and J. Matkala, “Nozzle Clogging Prediction in Continuous Casting of Steel,” 15th IFAC World Congress. Barcelona, Spain, 21-26 July. Oxford: Pergamon Press, pp. 143-147, 2002.
[8] S.K. Duggal, “Limit State Design of Steel Structures,” 2ndedn. New Delhi, India: McGraw Hill Education (India) Pvt. Ltd., pp. 8, 2014.
[9] K. Ramakrishna, K. Abhishek and R. Markandeya, “Effect of superheat on rim thickness in rimming steel ingots,” International Journal of Engineering Sciences and Research Technology (IJESRT), Vol. 5, Issue 4, pp. 60-74, 2016.
[10] United States Steel Corporation, Association of Iron and Steel Engineers and Lankford, W.T., “The Making, Shaping, and Treating of Steel” 10thedn. Warrandale: Association of Iron and Steel Engineers (AISE), pp. 749, 1985.
[11] O. Adaba,”Formation and evolution of Spinel in aluminum killed calcium treated linepipe,” Steels. Master’s thesis. Missouri University of Science and Technology, 2015. [Online]. Available at: https://scholarsmine.mst.edu/masters_theses/7455
[12] R.H. Tupkary and V.R. Tupkary, “An Introduction to Modern Steel Making,” 7thedn. Delhi, India: Khanna Publishers, pp. 405, 2011.
[13] K. Wunnenberg and J. Cappel, “Cost Saving Operation and Optimization on Metallurgical Reactions in BOF Practice,” AISTech-2008. Pittsburgh, USA, 5th-8th May. Warrandale: Association of Iron and Steel Technology (AIST), pp. 66-73, 2008.
[14] T. Kollmann, “Influence of bottom purging on the metallurgical results and the BOF process,” Master’s thesis. University of Leoben. 2010.[Online]. Available at: https://pure.unileoben.ac.at/portal/files/2469625/AC08230761n01vt.pdf
[15] R. Husken, P. Pottie, G. Guoguang and J. Cappel, “Overcoming the Conflict between Long BOF Refractory Lifetime and Efficient Bottom Stirring: A Case Study at Meishan Steel in China,” 45th Steelmaking Seminar – International. Porto Alegre, Brazil, 25th-28th May. (s.l.): Blucher, pp. 2286-2297, 2014.
[16] L. Holappa, “Recent Achievements in Iron and Steel Technology,” Journal of Chemical Technology and Metallurgy, Vol. 52, Issue 2, pp. 159-167, 2017.
[17] A.N. Conejo and D.E. Hernandez, “Optimization of AluminumDeoxidation Practice in the Ladle Furnace,” Materials and Manufacturing Processes, Vol. 21, Issue 8, pp. 796-803, 2007.
[18] K.C. Mills, L. Yuan And R.T. Jones, “Estimating the physical properties of slags,” The South African Institute of Mining and Metallurgy (SAIMM), Vol. 111, pp. 649-658, 2011.
[19] V. Sinelnikov And D. Kalisz, “Modeling Viscosity of Converter Slag,” Archives of Foundry Engineering, vol. 15, pp. 119-124, 2015.
[20] L. Zhang, B.G. Thomas, X. Wang and K. Cai, “Evaluation and Control of Steel Cleanliness-Review,” 85th Steelmaking Conference. Nashville, Tennessee, 10-13th March. Warrandale: Iron and Steel Society (ISS)-The American Institute of Mining, Metallurgical and Petroleum Engineers (AIME), pp. 431-452, 2002.
[21] N. Behera, A. Raddadi, S. Ahmad, N. Tewari and O. Zeghaibi, “ Use of Al-killed Ladle Furnace Slag in Si-killed Steel Process to Reduce Lime Consumption, Improve Slag Fluidity,” 10th International Conference on Molten Slags, Fluxes and Salts. Washington, USA, 22-25th May. Cham: Springer, pp. 1031-1039, 2016.
[22] O. Aydemir, “Use of Aluminium Dross for Slag Treatment in Secondary Steelmaking to Decrease Amount of Reducible Oxides in Ladle Furnace,” Master’s thesis. Middle East Technical University, 2007.[Online]. Available at: citeseerx.ist.psu.edu/viewdoc/download?doi=10.1.1.633.6397 &rep=rep1 &type=pdf
[23] A. Pasanen, “Online Control of Inclusion in Steelmaking,” Master’s thesis. Aalto University School of Chemical Technology, 2015.[Online]. Available at: https://aaltodoc.aalto.fi/bitstream/handle/123456789/17768/master_Pasanen_Asmo_2015.pdf?sequence=1&isAllowed=y
[24] P.C. Pistorius, “Slag carryover and the production of clean steel,” The South African Institute of Mining and Metallurgy (SAIMM), Vol. 119, Issue 6, pp. 557-561, 2019.
[25] A. Kamaraj, R. Saravanakumar and M. Rajaguru “State of the Art Control Measures for Aluminium Fade and SEN Clogging during Steelmaking Operations,” International Conferences on Advances in Metallurgy, Materials and Manufacturing (ICAMMM-2017). Salem, India, 6th-8th March. (s.l.): IOP Publishing, pp. 194-201, 2018.
[26] E.B. Pretorius and Baker Refractories (n.d.) ‘Fundamentals of EAF and Ladle Slags and Ladle Refining Principles’.
[27] Z. Deng and M. Zhu, “Deoxidation Mechanism of Al-Killed Steel during Industrial Refining Process,” ISIJ International, Vol.54, Issue 7, pp. 1498-1506, 2014.
You do not have rights to view the full text article.
Please contact administration for subscription to Journal or individual article.
Mail us at support@isroset.org or view contact page for more details.